Exploring the capacitor technologies needed in electric vehicles
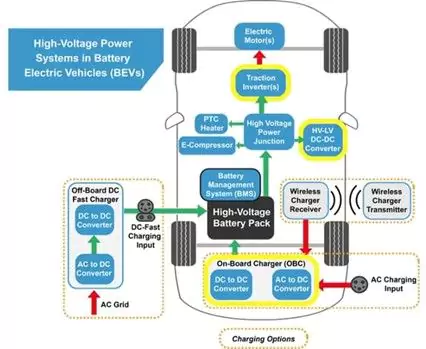
The electrical power systems in most modern technologies, like electric vehicles (EVs), are complex. In EVs specifically, power systems are responsible for performing many tasks such as converting AC to DC and DC to AC as well as managing changing power levels in DC/DC conversion. When performing these tasks, manipulating AC voltages and removing noise from DC voltage requires passive components such as capacitors, to perform many “jobs” inside the power system. But no single capacitor type can perform all these jobs since each one has different requirements for voltage, size, temperature, and reliability. Therefore, a variety of capacitor technologies, such as ceramic, film, and aluminum, are required to meet all these needs.
The roles capacitors play in EV power systems
Power systems within EVs must reliably handle large amounts of fluctuating power. While Figure 1 shows all the different functional blocks in an EV power system, we will focus specifically on the roles capacitors play in the following functions:
- Traction inverter (DC to AC)
- Onboard charger (AC to DC)
- DC/DC converter
Figure 1: A diagram highlighting the different functional blocks in a high-voltage power system in an EV. These are highlighted in yellow.
Traction Inverter
The function of an inverter is to convert DC power to AC. This function is commonly required in the traction inverter in an EV where battery DC is converted to AC for the motor. The major capacitor roles required here include the following:
Figure 2: A diagram of a traction inverter with the locations of the various capacitors called out.
On-Board Charger
An on-board charger takes AC power and converts it to DC to charge the battery. The major capacitor roles here include the following:
Figure 3: A diagram of an on-board charger with the locations of the various capacitors called out.
DC/DC Converter
The DC/DC converter takes the high-voltage battery power and converts it to a lower voltage. The major capacitor roles here include the following:
Figure 4. A diagram of a DC-DC converter with the locations of the various capacitors called out.
So now you’re probably wondering, of the different capacitor technologies, which one is the best option for each of these jobs? As mentioned, the type of capacitor technology you will need depends on the specific voltage, size, temperature, and reliability requirements of the application, but there are some overall trends we are seeing:
- Film and aluminum are typically used for DC link capacitors
- Film and MLCCs are typically used for filtering capacitors
- Film and MLCCs are typically used for resonant capacitors
- Film and MLCCs are typically used for snubber capacitors